In gesprekken met directeuren en managers in de metaalindustrie hoor ik vaak dezelfde vragen:
"Welk ERP-systeem moeten we aanschaffen?"
"Is deze MES-oplossing geschikt voor onze fabriek?"
"Kunnen we met deze machine voldoen aan de eisen van Industrie 4.0?"
Deze vragen zijn begrijpelijk, maar ze vertrekken vanuit een fundamenteel verkeerd uitgangspunt.
De juiste vragen stellen
In plaats van te beginnen bij softwarepakketten en merknamen, zou de eerste vraag moeten zijn:
- "Wat willen we eigenlijk bereiken in onze bedrijfsprocessen?"
- "Welke knelpunten ervaren we momenteel?"
- "Hoe willen we dat onze verschillende systemen met elkaar communiceren?"
Door deze vragen voorop te stellen, creëer je een heel ander perspectief op digitalisering – eentje die niet oplossingsgedreven is, maar technologiegedreven.
Dit inzicht is niet overnight gekomen. Het is gevormd door een combinatie van:
- Praktijkervaring bij tientallen metaalbedrijven
- Uitwisseling met internationale experts
- Hands-on werken met open communicatieprotocollen
Een belangrijke inspiratiebron was Walker Reynolds van 4.0 Solutions, wiens lessen over industriële connectiviteit en Minimum Technische Eisen mijn visie hebben verscherpt. Via mijn Smart Metals Podcast heb ik gesprekken gevoerd met toonaangevende experts, die mij steeds weer bevestigden dat technologie-infrastructuur belangrijker is dan individuele softwarepakketten.
De praktische kennis heb ik opgedaan door te werken met connectiviteitsplatformen zoals Ignition en United Manufacturing Hub, waarbij ik ontdekte hoe krachtig het is wanneer systemen via open standaarden als MQTT met elkaar communiceren. Deze platforms maken concreet wat eerder theoretisch leek: een volledig verbonden fabriek waarin informatie naadloos stroomt.
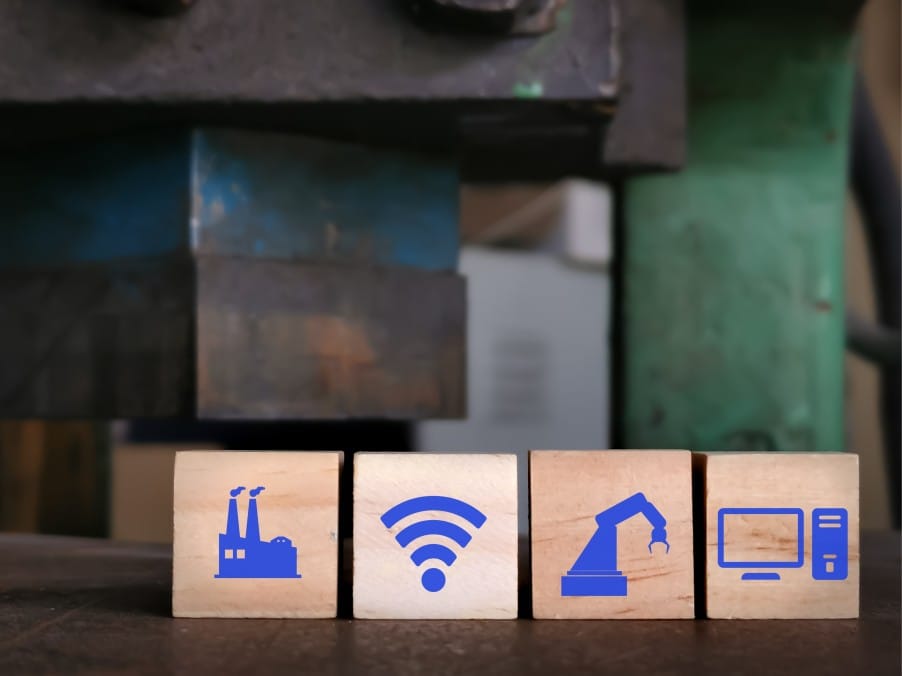
De valkuil van puur oplossingsgedreven denken
Veel metaalbedrijven benaderen hun digitaliseringsstrategie vanuit het perspectief van kant-en-klare oplossingen. Ze laten hun bedrijfsprocessen vaak aansluiten bij de functionaliteiten van een gekozen softwarepakket, in plaats van andersom.
Deze oplossingsgedreven aanpak zien we in verschillende patronen:
- Geïntegreerde ERP-systemen implementeren in de verwachting dat deze alle bedrijfsprocessen kunnen coördineren
- Machines aanschaffen met bijgeleverde software die vaak prima werkt, maar beperkte communicatiemogelijkheden heeft met andere systemen
- MES-pakketten inzetten met standaard workflows die niet altijd passen bij de unieke processen van het bedrijf
De uitdagingen van deze aanpak worden pas zichtbaar wanneer het bedrijf verder wil ontwikkelen:
- Koppelingen tussen verschillende systemen vragen vaak extra inspanning
- Informatie-uitwisseling tussen verschillende leverancierssystemen is niet altijd optimaal
- De flexibiliteit om snel op veranderingen in te spelen kan beperkt zijn
Het is belangrijk om te benadrukken: deze softwarepakketten zijn op zichzelf uitstekende producten met veel functionaliteit. Het probleem ontstaat niet door de kwaliteit van de individuele oplossingen, maar door hoe ze samen (niet) werken in een heterogene omgeving.
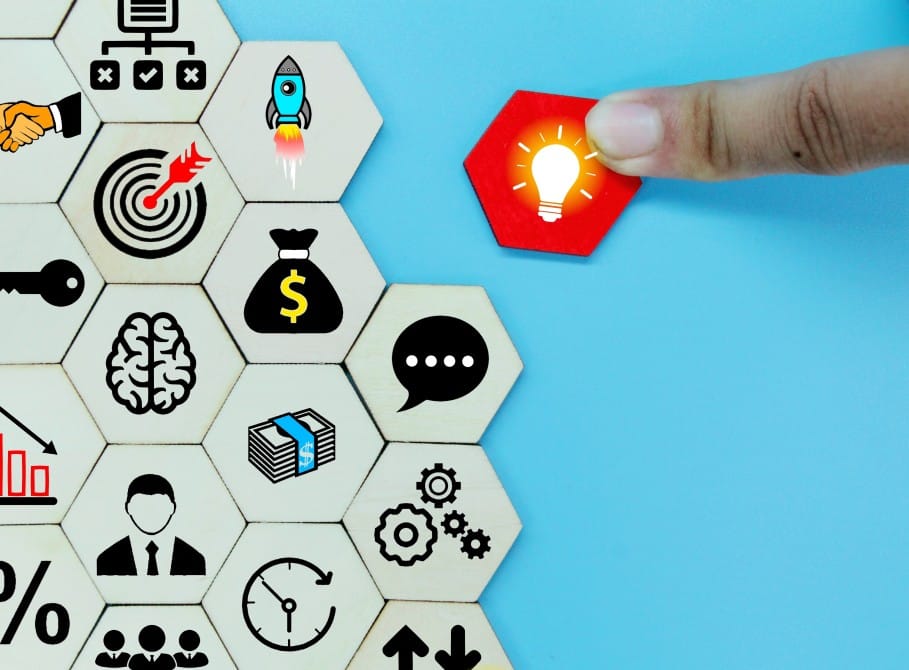
Begrippenkader: Een korte uitleg van industriële software
Om de problematiek beter te begrijpen, is het nuttig om enkele veelgebruikte termen in de industriële automatisering te verhelderen:
ERP (Enterprise Resource Planning)
Uitgebreide softwaresystemen primair gericht op het afhandelen van administratieve processen: boekhouding, inkoop, verkoop, voorraad en projectregistratie. ERP-systemen zijn ontworpen om bedrijfsmiddelen te plannen en beheren op strategisch niveau.
MES (Manufacturing Execution System)
Deze systemen vormen de brug tussen planningswereld en operationele productieomgeving. Ze sturen de productie op de werkvloer aan, monitoren voortgang, bewaken kwaliteit en verzamelen productiedata. Een goed MES vertaalt bedrijfsdoelen naar concrete productieorders.
SCADA (Supervisory Control And Data Acquisition)
Controlesystemen die realtime data verzamelen van machines en processen, meestal via PLC's. SCADA-systemen visualiseren operationele gegevens en stellen operators in staat productieprocessen te monitoren en bij te sturen.
HMI (Human Machine Interface)
De aanraakschermen, bedieningspanelen en visualisaties die operators gebruiken om direct met machines te communiceren. Ze vormen de brug tussen mens en machine op de werkvloer.
IIoT (Industrial Internet of Things)
Het netwerk van verbonden industriële apparaten, machines en sensoren die data kunnen verzamelen en uitwisselen. IIoT maakt real-time monitoring, analyse en optimalisatie van productieprocessen mogelijk.
MTE (Minimum Technische Eisen)
Een specifieke set technische minimumeisen waaraan moderne industriële systemen moeten voldoen om toekomstbestendig en interoperabel te zijn. Deze worden later in dit artikel verder toegelicht.
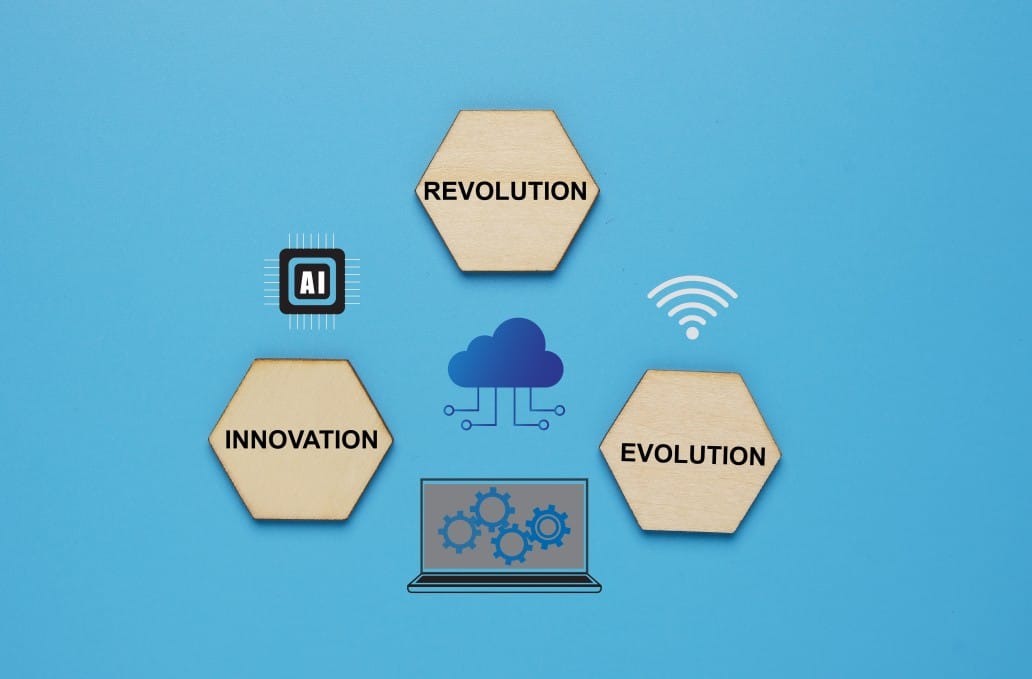
De kruisweg van digitalisering in metaalbedrijven
Misschien herken je dit in je eigen bedrijf:
✓ Je hebt een ERP-systeem, maar werkorders worden alsnog uitgeprint en overgetypt in andere systemen
✓ Je programmeurs besteden uren aan het verzamelen van informatie die al ergens in je bedrijf aanwezig is
✓ Je hebt verschillende machines met elk hun eigen besturingssoftware, die niet met elkaar communiceren
✓ Je planning is een constante uitdaging omdat informatie niet tijdig beschikbaar is
Deze dagelijkse frustraties zijn geen tekortkomingen van jouw organisatie. Ze zijn het rechtstreekse gevolg van een benadering die de industrie jarenlang heeft gevolgd: een focus op individuele oplossingen in plaats van op verbindende technologie.
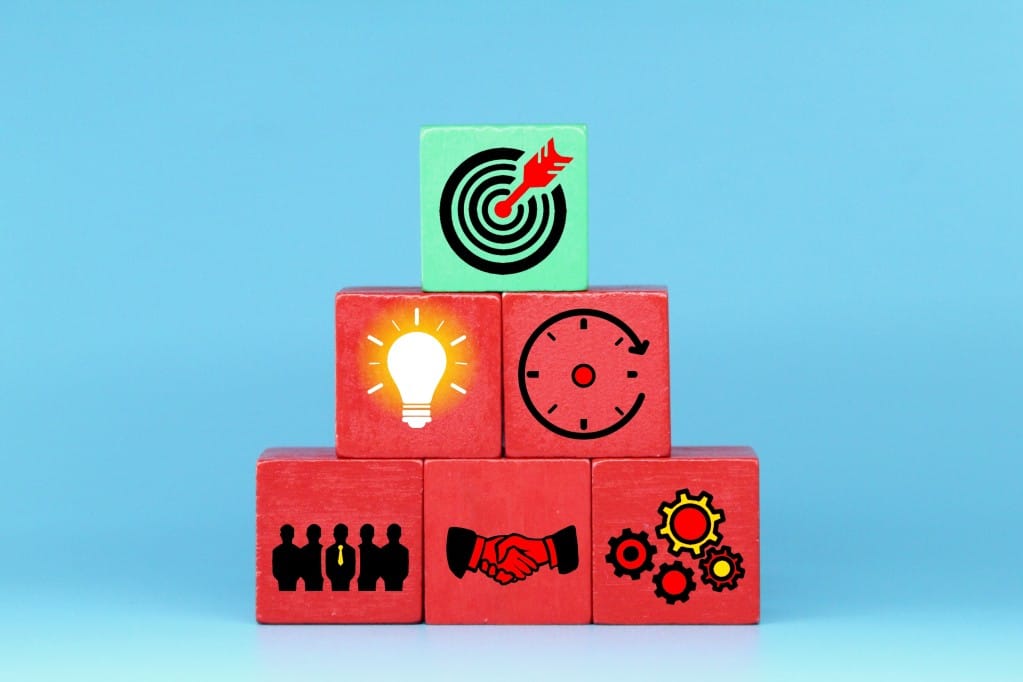
Oplossingen vs. Technologie: Een fundamenteel andere benadering
De oplossingsgedreven aanpak
Wat bedoel ik met "oplossingen"? Hieronder vallen de gespecialiseerde softwarepakketten en producten die leveranciers aanbieden:
- ERP-systemen zoals MKG, Ridder iQ of SAP die uitgebreide functionaliteit bieden
- Machines van fabrikanten zoals TRUMPF, Bystronic of LVD met hun eigen softwaresystemen
- MES-pakketten die gericht zijn op werkvloerbesturing
- CAD/CAM-software die steeds rijkere functionaliteit biedt voor design en productie
Deze systemen zijn stuk voor stuk krachtige tools, ontwikkeld door experts die hun domein door en door kennen. Ze bieden veel waarde en zijn essentieel voor moderne productieomgevingen. De uitdaging zit niet in de kwaliteit van deze oplossingen, maar in hoe ze samen functioneren binnen het grotere ecosysteem van een metaalbedrijf.
Een bijzonder uitdagend punt voor Nederlandse plaatwerkers: verschillende machinefabrikanten leveren hun eigen CAM-software als optimale oplossing voor hun specifieke machines. Heb je meerdere merken machines? Dan krijg je meerdere CAM-systemen, elk geoptimaliseerd voor hun eigen machines maar met eigen werkwijzen. Dit leidt tot praktische vragen: Welk systeem maakt de uitslag? Wie genereert de CNC-code? Hoe zorg je voor een consistente methodiek?
De verborgen uitdagingen van een puur oplossingsgedreven aanpak
Hoewel op oplossingen gebaseerde digitalisering aantrekkelijke voordelen biedt (één leverancier, één aanspreekpunt), ontstaan er met de tijd enkele uitdagingen:
- Leveranciersafhankelijkheid: Je bedrijf wordt steeds meer afhankelijk van het ecosysteem van één leverancier, met beperktere onderhandelingsruimte bij vernieuwingen.
- Integratie-inspanning: Deze systemen werken uitstekend binnen hun eigen domein, maar vereisen vaak extra inspanning voor optimale samenwerking met oplossingen van andere leveranciers.
- Schaalbaarheidsoverwegingen: Naarmate je bedrijf groeit of diversifieert, kunnen de grenzen van wat binnen één systeem mogelijk is zichtbaar worden.
- Complexiteit vs. flexibiliteit: Alles-in-één-oplossingen zijn vaak óf rijker aan functionaliteit dan kleinere bedrijven nodig hebben, óf niet specifiek genoeg voor gespecialiseerde processen.
- Aanpassingskosten: Maatwerk blijft vaak nodig bij veranderende bedrijfsbehoeften, wat kan leiden tot een langdurige relatie met de leverancier.
Stel je een situatie voor: je hebt geïnvesteerd in een hoogwaardig ERP-systeem, maar toch printen je programmeurs nog steeds orders uit om ze over te typen in hun CAM-software. Dit kost waardevolle tijd – tijd die ze beter kunnen besteden aan het optimaliseren van bewerkingen voor betere kwaliteit en lagere kosten.
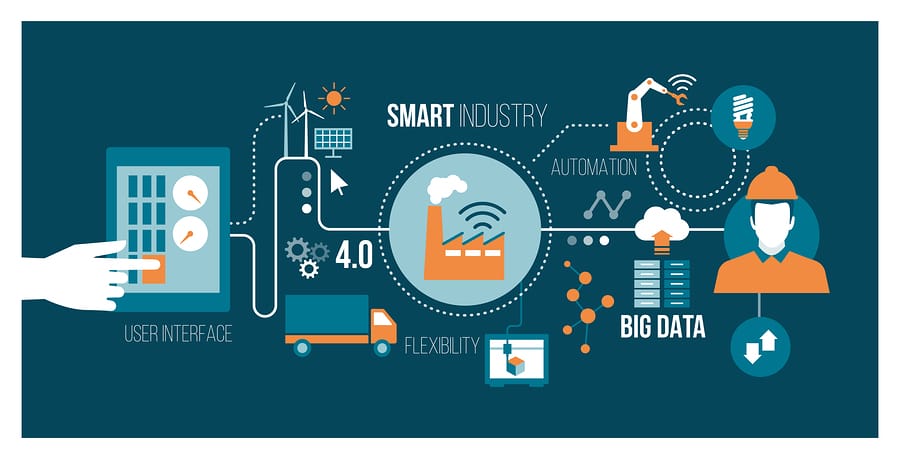
De technologiegedreven aanvulling
In plaats van te starten bij afzonderlijke oplossingen, begint technologiegedreven werken bij de fundamentele vraag: hoe zorgen we dat informatie naadloos door het bedrijf stroomt, terwijl we de sterke punten van specialistische software behouden?
Bij deze aanpak focussen we op:
- Open communicatiestandaarden zoals REST APIs en MQTT, die systemen van verschillende leveranciers laten samenwerken
- Datasoevereiniteit: Je bedrijfsgegevens blijven van jou, in formaten die niet gebonden zijn aan één leverancier
- Een verbindingslaag die fungeert als het zenuwstelsel van je digitale infrastructuur, waaraan alle systemen kunnen koppelen
- Minimum Technische Eisen (MTE) voor elk nieuw systeem dat je aanschaft
Met deze benadering erken je dat verschillende afdelingen verschillende gespecialiseerde tools nodig hebben – programmeurs hebben CAD/CAM nodig, administratie werkt in ERP, planners gebruiken specifieke planningstools – en je zorgt dat deze tools effectief communiceren via een gemeenschappelijke taal.
Het gaat er niet om gespecialiseerde software te vervangen, maar om deze te verbinden in een coherent ecosysteem waarin informatie vrij kan stromen.
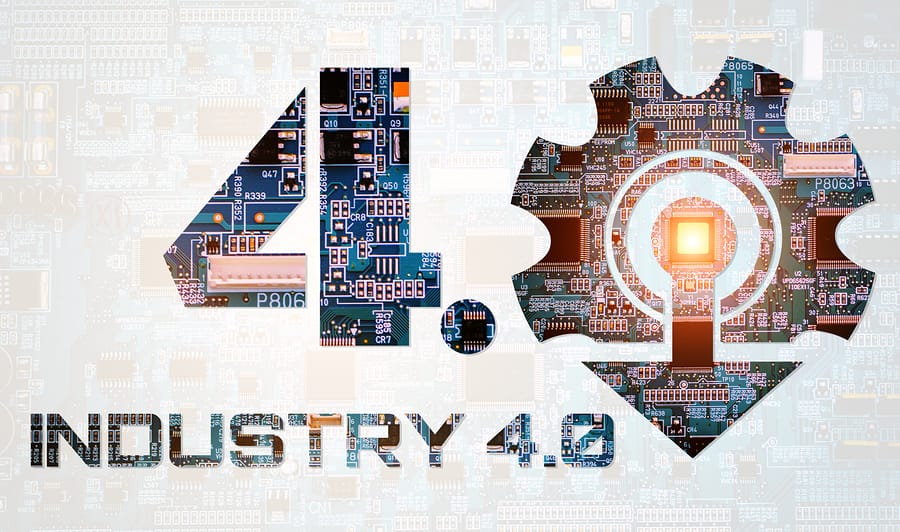
De bouwstenen van een verbonden metaalbedrijf
Een moderne technologiegedreven infrastructuur in een metaalbedrijf bestaat typisch uit:
- Een message broker (vaak MQTT): Het hart van het systeem, een lichtgewicht berichtendienst waarop alle systemen kunnen publiceren en abonneren. Wanneer een orderwijziging plaatsvindt in ERP, wordt dit direct gepubliceerd en ontvangen door alle geabonneerde systemen (CAD/CAM, planning, etc.)
- Dataopslag in open formaten: Jouw gegevens blijven van jou, toegankelijk via standaard interfaces en niet opgesloten in leveranciersspecifieke databases
- Historian: Een systeem dat alle gebeurtenissen en wijzigingen registreert voor analyse en traceerbaarheid
- Replica's: In-memory kopieën van veelgebruikte gegevens (zoals actuele orders, machine-instellingen) voor snelle toegang en zoekopdrachten
- Connectoren: De "vertalers" die bestaande systemen verbinden met je centrale infrastructuur
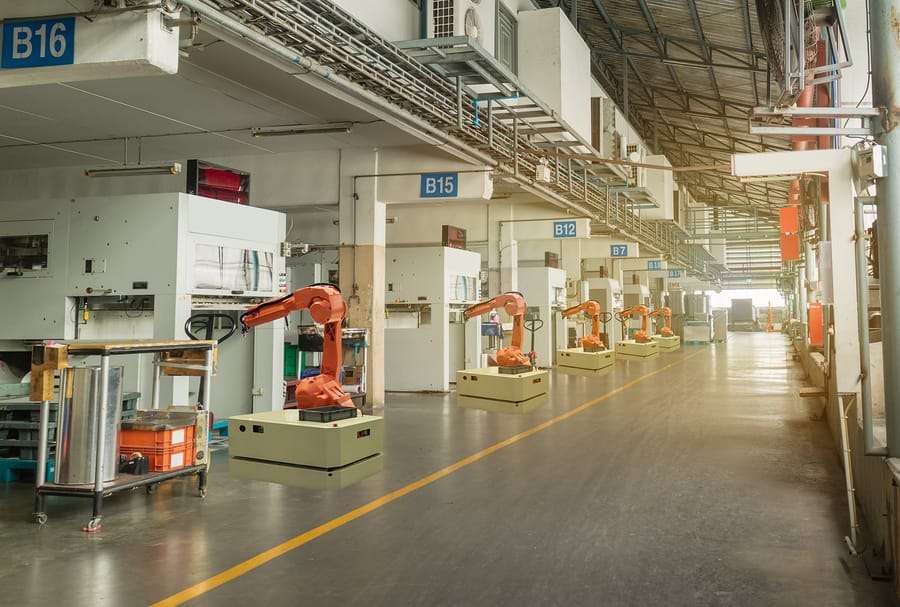
Wat betekent dit in de dagelijkse praktijk?
Een technologiegedreven plaatwerkerij zou in de praktijk zo kunnen werken:
- Een klant plaatst een order, die wordt vastgelegd in ERP
- Het ERP publiceert deze order automatisch naar de message broker
- CAD/CAM-systemen ontvangen direct de relevante informatie
- Programmeurs zien nieuwe orders verschijnen in hun werklijst, compleet met alle benodigde gegevens
- Zodra programma's gereed zijn, wordt dit gepubliceerd naar de broker
- Planners en productieleiders ontvangen direct een notificatie
- Machines rapporteren hun status en voortgang automatisch terug
Geen handmatige overdrachten. Geen dubbele invoer. Geen zoektochten naar informatie.
Stel je voor: een metaalbedrijf implementeert deze aanpak en kan daardoor de administratieve overhead voor programmeurs drastisch verminderen. Voor het eerst in jaren zou er geen achterstand meer zijn in de werkvoorbereiding.
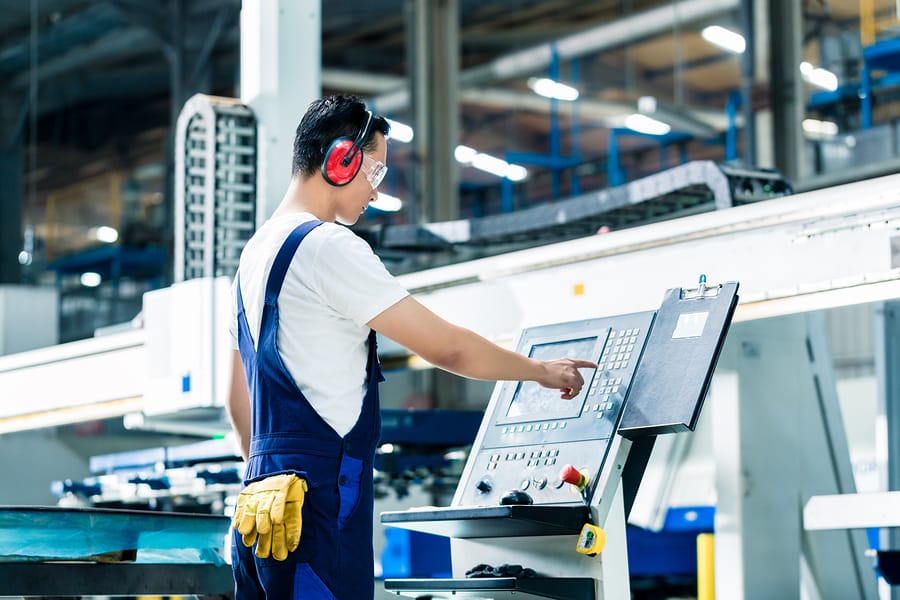
De concrete voordelen
Technologiegedreven werken biedt metaalbedrijven tastbare voordelen:
- Flexibiliteit: Je kunt de beste tools kiezen voor elke taak, zonder zorgen over compatibiliteit
- Toekomstbestendigheid: Nieuwe technologieën of machines kunnen eenvoudig worden geïntegreerd in je bestaande omgeving
- Kostenefficiëntie: Minder afhankelijkheid van één leverancier betekent betere onderhandelingspositie en lagere mutatiekosten
- Snelheid: Informatie stroomt automatisch naar waar deze nodig is, zonder vertragingen of handmatige tussenkomst
- Datagedreven inzichten: Wanneer alle informatie centraal beschikbaar is, kun je patronen herkennen en processen optimaliseren
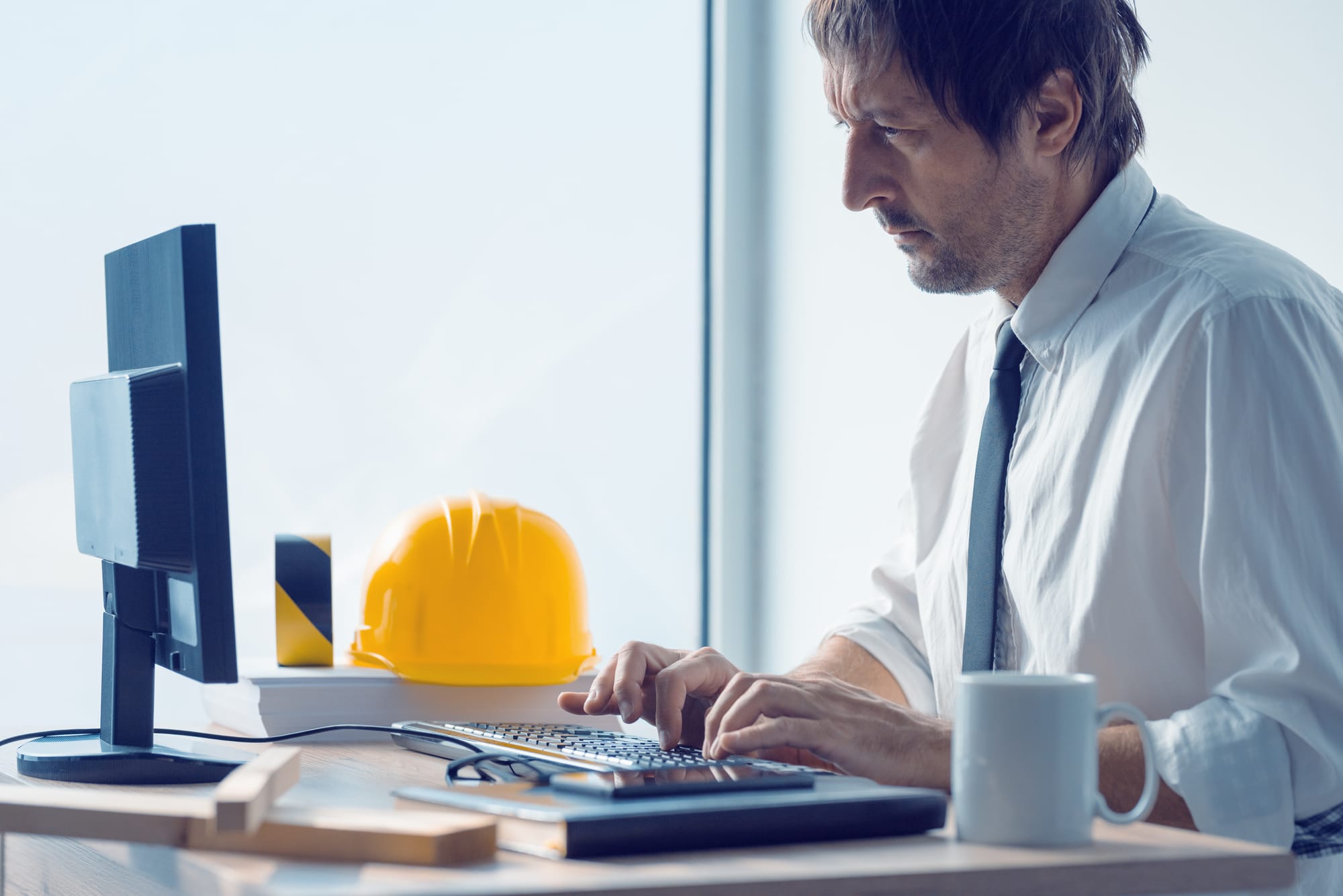
Minimum Technische Eisen: Je digitale kwaliteitsstandaard
Om technologiegedreven te werken, is het essentieel om minimale eisen te stellen aan elk nieuw systeem dat je aanschaft. Deze Minimum Technische Eisen (MTE) fungeren als een "digitale kwaliteitsstandaard" en omvatten:
- Edge-gedreven: Systemen moeten data direct bij de bron kunnen capteren en delen
- Report by exception: Alleen relevante wijzigingen worden doorgegeven, niet constant alle data
- Lichtgewicht: Geen zware infrastructuureisen of complexe installaties
- Open connectiviteit: Communicatie via algemeen erkende standaarden (REST, MQTT, OPC-UA)
Bij aankoop van nieuwe machines of software zou je deze eisen expliciet moeten opnemen in je programma van eisen. Leveranciers die hier niet aan kunnen voldoen, vallen af – ongeacht hoe indrukwekkend hun functionaliteit lijkt.
Voor wie is technologiegedreven werken geschikt?
Eerlijk gezegd: niet voor ieder metaalbedrijf. Deze aanpak is vooral waardevol voor:
- Bedrijven met machines van meerdere leveranciers
- Organisaties die snelheid en flexibiliteit als concurrentievoordeel zien
- Ondernemingen met ambitie om te groeien of te innoveren
- Bedrijven die worstelen met informatiestromen tussen afdelingen
Voor zeer kleine bedrijven met eenvoudige processen of voor bedrijven die volledig binnen één leveranciersecosysteem opereren, kan een oplossingsgedreven aanpak volstaan.
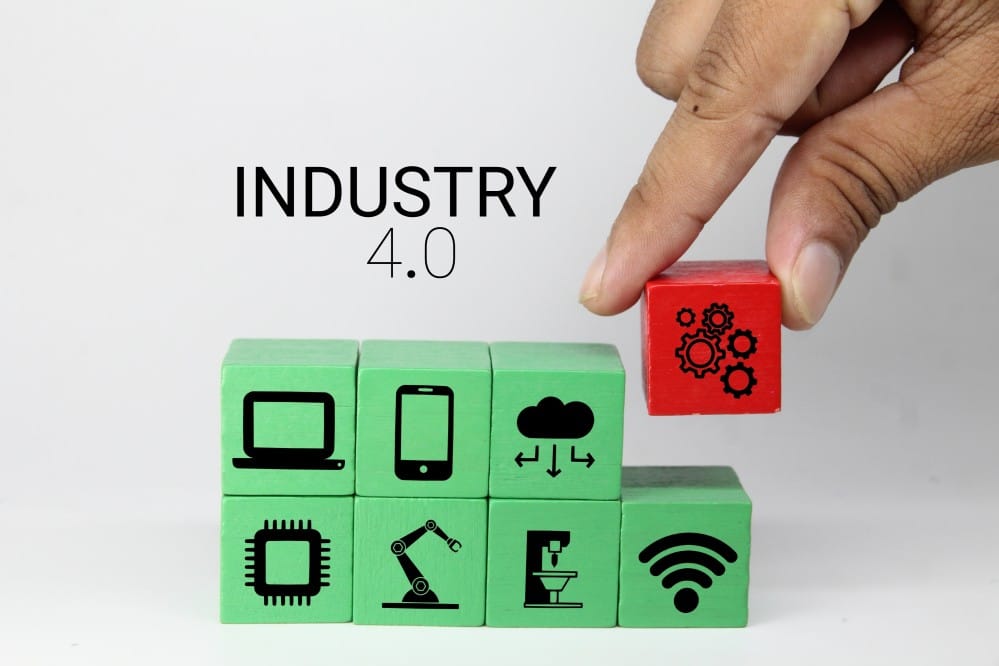
Hoe begin je? Praktische eerste stappen
De transitie naar technologiegedreven werken hoeft niet radicaal te zijn. Je kunt beginnen met kleine, gerichte verbeteringen:
- Breng je informatiestromen in kaart: Waar blijft informatie hangen? Welke handmatige overdrachten veroorzaken vertragingen?
- Definieer je Minimum Technische Eisen: Welke eisen stel je aan toekomstige systemen? Documenteer dit als onderdeel van je inkoopbeleid.
- Start met één pijnpunt: Kies de informatieoverdracht die de meeste vertraging of fouten veroorzaakt en los deze op met een gerichte integratie.
- Bouw expertise op: Investeer in kennis over moderne integratietechnologieën, of werk samen met partners die deze expertise hebben.
- Creëer een technologieroadmap: Plan hoe je stapsgewijs naar een volledig verbonden infrastructuur toewerkt.
Stel je voor: een metaalbedrijf begint met het automatiseren van de informatieoverdracht van ERP naar CAD/CAM-systemen. Dit zou direct uren per week aan programmeurstijd kunnen opleveren – mogelijk genoeg om de investering binnen enkele maanden terug te verdienen. Vervolgens zou het bedrijf stap voor stap kunnen uitbreiden naar andere koppelingen.
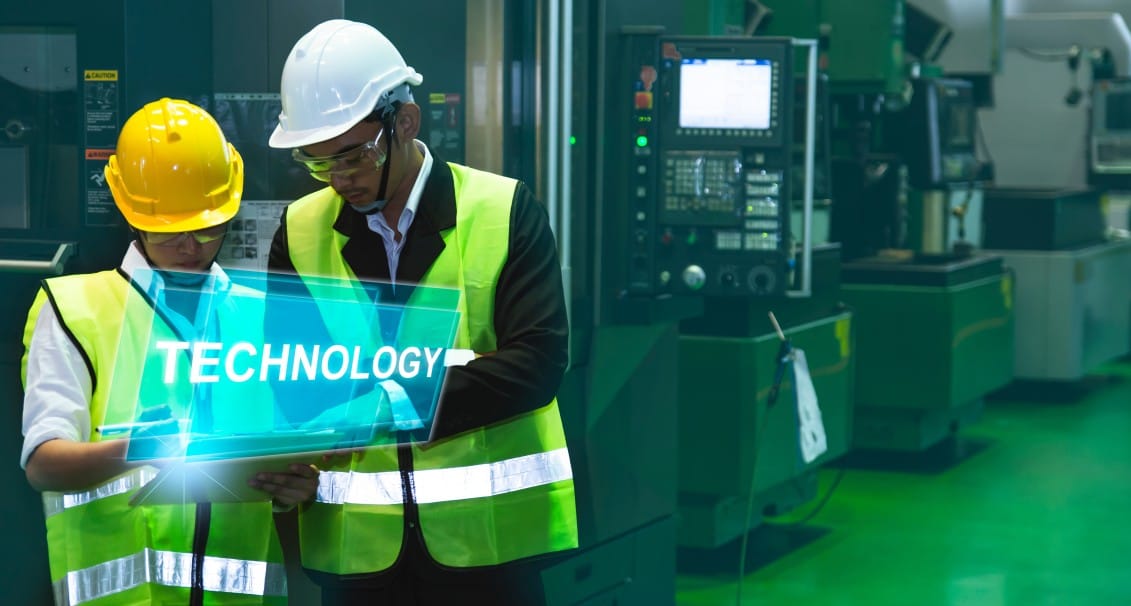
Van wie is jouw digitale toekomst?
De keuze tussen een puur oplossingsgedreven of een technologiegedreven aanpak is fundamenteel: het bepaalt in welke mate je als metaalbedrijf zelf de koers van je digitale ontwikkeling kunt bepalen.
In een markt waarin flexibiliteit, snelheid en aanpassingsvermogen cruciale concurrentiefactoren zijn, is het steeds belangrijker om een balans te vinden. De ideale aanpak combineert het beste van beide werelden:
- De diepgaande expertise en functionaliteit van gespecialiseerde softwareoplossingen
- De flexibiliteit en toekomstbestendigheid van een open technologische infrastructuur
Door te investeren in een verbindende technologische infrastructuur bouw je niet alleen aan efficiëntere processen voor vandaag, maar ook aan een flexibel fundament waarop je kunt blijven innoveren voor morgen, terwijl je optimaal gebruik blijft maken van de krachtige oplossingen die softwareleveranciers bieden.
De vraag is niet óf oplossingen belangrijk zijn - dat zijn ze zeker - maar hoe je ze verbindt tot een coherent geheel dat meer is dan de som der delen.
Credits / over SMC:
De inzichten in dit artikel zijn gevormd door mijn ervaringen als digitaliserings-consultant in de Nederlandse metaalindustrie, geïnspireerd door de lessen van pioniers zoals Walker Reynolds van 4.0 Solutions. Voor meer informatie over dit onderwerp, beluister ook mijn Smart Metals Podcast, waar we regelmatig experts op dit gebied interviewen.
Plan een vrijblijvend gesprek om te bespreken hoe jouw metaalbedrijf een evenwichtige benadering kan vinden tussen krachtige softwareoplossingen en een flexibele technologische infrastructuur.